In The News
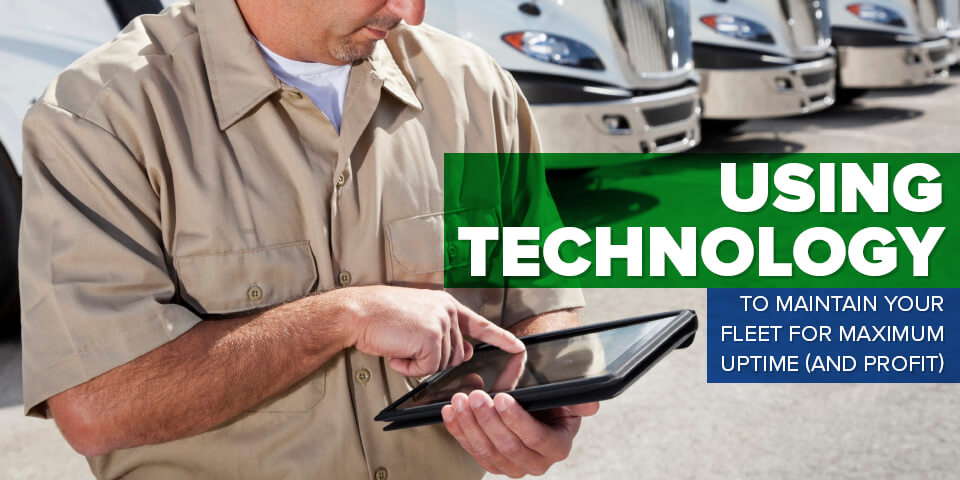
Using Technology to Maintain Your Fleet for Maximum Uptime (and Profit)
As a fleet owner, you want to keep your trucks rolling and making money for you and your drivers—and not sitting on the side of the road or in the shop.
But, as your fleet grows, it can be challenging to keep track of maintenance schedules and repairs, especially with trucks spread out across the country. And if you or your drivers don't stay on top of the maintenance and repairs when they're needed, you'll be dealing with unplanned downtime that can cost you a lot of money.
So, how can you use technology to help you maintain your fleet more efficiently and effectively? EO recently spoke with fleet owners Rob Ahlers and Susan Medlin. Here are some ideas they shared.
Rob Ahlers
Company: MSR Transport Services
Fleet Size: 6 tractors; planning on adding 3 more tractors in 2018.
What technologies do you use for managing maintenance?
“We currently do not use any of the onboard telematics or Detroit systems, but the new tractors we just ordered from Western Star will be equipped with the Detroit Virtual Technician. We have also instituted a simple spreadsheet with each tab representing a truck, named by VIN (vehicle identification number), and we have the complete maintenance history there for quick reference. And we use a calendar app that we share with the drivers, and it pushes notifications to the drivers when maintenance items are due.”
What calendar app do you use?
“The calendar app is ‘TeamUp’ (see https://www.teamup.com/), and it is great. We have a calendar for each tractor and then one for [action items], maintenance, and so forth. When we put in an event, like a tractor PM (preventive maintenance) due, we can put it on multiple calendars—on the tractor calendar which is shared with the drivers, and our maintenance calendar where we can see all maintenance actions at one time. The drivers can create events and add items to it, like when they perform a minor light bulb replacement, windshield replacement, or PM before the scheduled one."
What has been the impact?
“Using the spreadsheet and calendar has helped me work with our drivers to have them be more efficient and make better decisions when it comes time to perform maintenance. They can see when an item is due and schedule it for home time or when they have a lull in a weekend. We have found since doing this, that we are no longer pushing the limits and getting maintenance performed at the last minute.”
Susan Medlin
Company: Medlin Expedited and Leasing LLC
Fleet Size: 15 trucks, planning on adding 5 more vehicles in 2018
What technologies do you use for managing maintenance?
“I think the most crucial technology we use is through Detroit Diesel—Virtual Technician. The system will alert me if there's a ‘fault code’ on the truck, letting me know if there is something wrong with the truck usually before the driver even knows. This way, we can get ahead of the situation and get the truck fixed before we have a failure.”
What was it like before you had to the technology to send you “fault code” alerts?
“We were at the mercy of wherever the truck broke down. And if it broke down, you had fewer choices. You had to tow it to the nearest location that could service the truck under warranty—and that shop could be backed up with a long wait time.”
What has been the impact?
"Now, we get a warning with a time range attached to it, so we have an idea of how critical that failure is, which gives us more options to respond more effectively. For example, if we have a truck coming out of Laredo and receive an alert that the truck is having issues, that alert will give us an idea of how urgent that issue is. This way, we can call ahead to a repair shop en route to see how backed up they are. In fact, we can call several places to see who can work our truck in and get it looked at the quickest to minimize the downtime. The impact is that we can now get more control over the situation before the truck has a catastrophic failure."